HAYNES 25 (L605)
Haines 25 is a cobalt alloy with good formability and excellent high temperature properties. At 1800°F, Haynes 25 sheet has a 100 hour stress fracture strength of 7000 psi. This alloy is resistant to oxidation and carburization up to 1900°F.
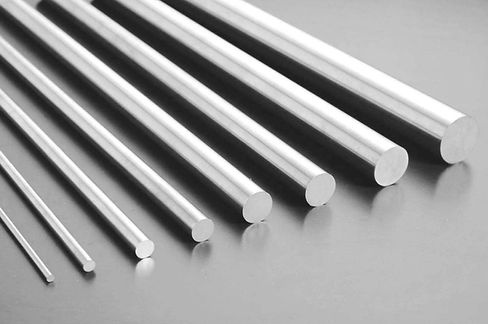
Type Analysis

Applications
The Haynes 25 has provided good service on many jet engine parts. Some of these include turbine blades, combustion chambers, afterburner parts and turbine rings. The alloy has also been used successfully in a variety of industrial furnace applications, including furnace muffles and liners, which are critical points in high-temperature kilns.
Corrosion Resistance
Haynes 25 (L-605) has excellent resistance to the hot corrosive atmospheres encountered in certain jet engine operation. Oxidation resistance is suitable for intermittent service up to 1600°F and continuous service up to 2000°F.
Haynes 25 (L-605) is highly resistant to scaling and oxidation at high temperatures, and has particularly good qualities under extreme oxidizing conditions.
The material also has good resistance to chemical oxidizing agents and to hydrochloric and nitric acids at certain concentrations and temperatures. Very good resistance to salt spray corrosion.
Heat Treatment
Heat-treated solution for optimum properties
For optimum properties, most processed products are shipped in solution heat treated. These alloys are typically annealed in a temperature range of 2150 to 2250°F and then either rapidly air cooled or quenched. Sheets up to 0.025" thick are solution heat treated, rapid air cooled, or water quenched at 2150°F; 0.026" and larger, air cooled or feed cooled at 2200°F, plate at 2200°F, bar, feed water at 2250°F Cooling.
Improvement of room temperature and room temperature characteristics due to cold construction and aging
Proper cold working and aging will improve the thermal tensile strength of both indoor and Haynes 25 sheets. A moderate amount of cold work increases creep strength up to 1800°F and stress rupture strength up to 1500°F. Aging doesn't bring much benefit. However, strain aging from 700 to 1100°F improves creep and burst strength below 1300°F.
